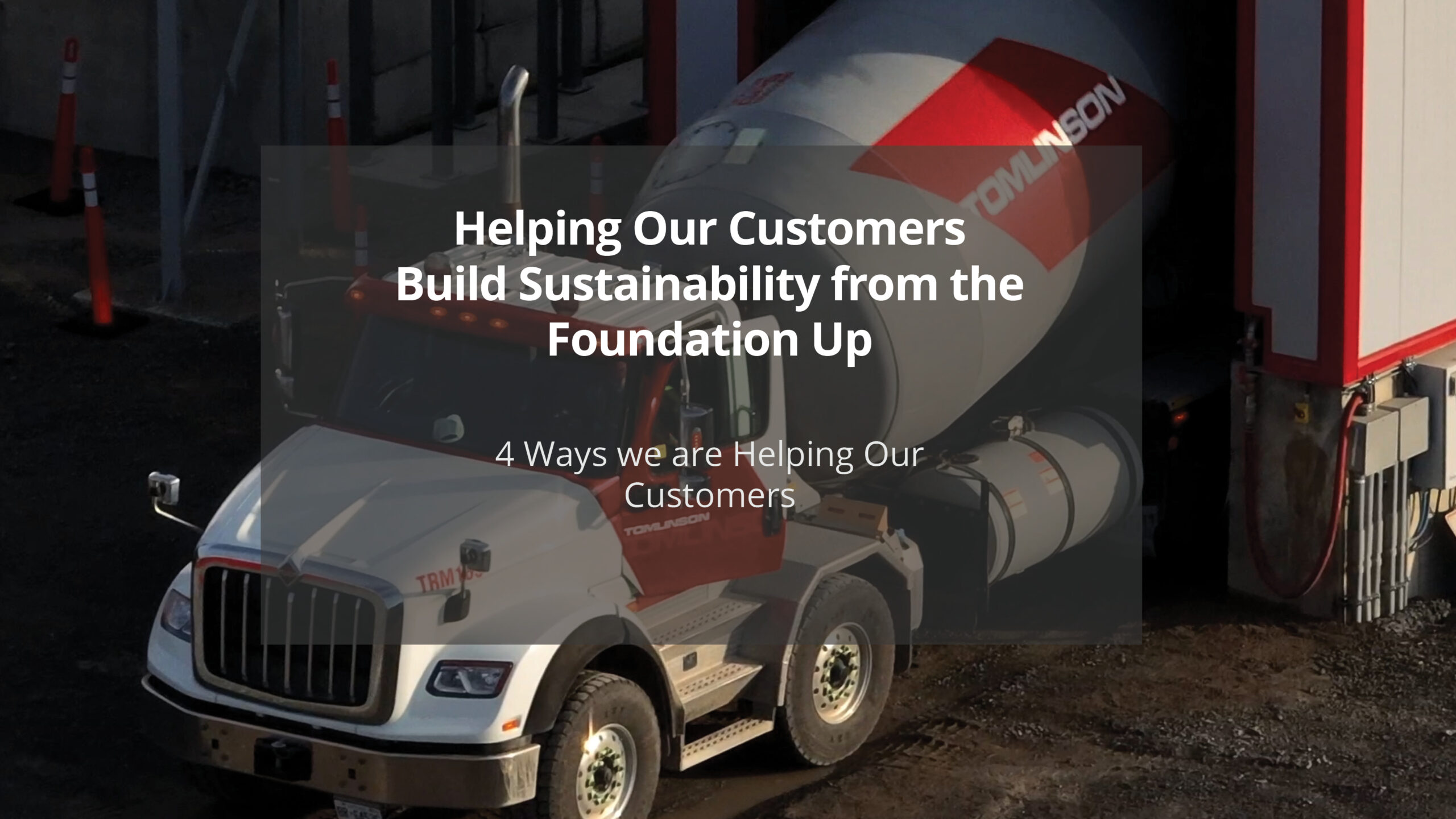
Helping Our Customers Build Sustainability from the Foundation Up
Tomlinson Ready Mix is dedicated to helping customers build sustainability from the foundation up by offering innovative and low carbon intensive mixes. By using materials like gul cement, supplementary cementitious materials, and advanced admixtures, the team ensures high-quality, durable, and sustainable concrete with reduced carbon emissions. By providing type III environmental product declarations for all mixes, customers can make informed decisions aligned with their sustainability goals.
As our customers seek ways to minimize the environmental impact of their projects, our Tomlinson Ready Mix team is continuously researching, testing and implementing innovative methods and technologies. Enabling our team to offer customers the option of sustainable concrete mixes, without compromising durability.
Here are a few of the ways our team creates low-carbon concrete:
Maintaining Quality While Reducing Emissions
One of the main ingredients of concrete is cement, which utilizes a process that heats limestone to over 1300oC in a kiln to produce clinker. This process releases carbon dioxide as a byproduct. To reduce carbon emissions at this stage, we can use GUL cement.
General Use Limestone (GUL) Cement is an eco-friendly alternative that uses a higher amount of raw limestone dust. GUL cement uses the same materials as GU cement but with less clinker, a higher limestone content results in a product that works the same, measures the same and performs the same, but the CO2 emission are reduced. By using GUL cement, you can reduce CO2 emissions by 10–15%.
Supplementary Cementitious Materials
Supplementary Cementitious Materials play a crucial role in optimizing the performance of concrete in various ways. Fly ash, for instance, not only improves the fluidity of cement but also reduces shrinkage cracking, resulting in a more durable structure.
Silica fume and slag are known to boost the strength of concrete significantly, enhancing characteristics such as compressive, flexural, and tensile strength. Silica fume, in particular, offers additional benefits such as increased resistance to chemically-aggressive environments and prevention of alkali-silica reactions that can harm concrete structures.
By incorporating these materials into concrete mixes, you are not only enhancing the performance your concrete, but your mix will also be more sustainable. These materials have a considerable impact on reducing carbon emissions in concrete production and using these materials recycles products from other industries that would otherwise be sent to landfills.
- Slag is a bi-product of steel production.
- Silica-fume is a bi-product of the silicon electronics industry.
- Fly ash is a bi-product of the coal power- plant industry.
By using these supplementary cementing materials, we can divert them from landfills and reduce our environmental impact, all while improving the performance of our concrete.
Admixtures
Admixtures play a crucial role in optimizing concrete performance. For example, strength-enhancing agents react at a microscopic level with unused and bi-product molecules. From the initial cement reaction these admixtures are chemically controlled, they provide a repeatable and controlled strength enhancement to the concrete.
By utilizing modern additives such as strength-enhancing agents and superplasticizers, we can enhance concrete strength and make it more sustainable. This not only improves the quality of the concrete, but it also helps us achieve a reduction in carbon emissions. We stock a variety of advanced admixtures at our ready-mix plants and incorporate them into our projects where we can ultimately help our customers reach their sustainability goals.
Type III EPD’s
Tomlinson Ready Mix is proud to offer Type III (third-party audited and approved) Environmental Product Declarations (EPDs) for all concrete mixes supplied from our plants. These EPDs provide the Global Warming Potential (GWP), empowering stakeholders to select concrete mixes that align with specific project requirements. By collaborating with contractors, consultants, owners, and other invested parties, we can assist in establishing and attaining targeted carbon budgets. Leveraging our Type III EPDs, we can conduct comparisons against industry-standard mix designs in Ontario, ensuring superior GWP savings that surpass industry averages.
We pride ourselves in leading the industry in innovation by incorporating technologies that allow us to provide sustainable solutions to meet and exceed our customers’ needs. Contact us now if you want to learn more about how we can help you meet your project sustainability goals.